In modern automotive manufacturing, the transmission shaft, as a core component of the power transmission system, directly impacts vehicle performance through its machining precision and efficiency. Recently, we successfully developed a custom step drill for a well-known automotive parts manufacturer, specifically designed for machining stepped installation holes in 10CrMo11 nitrided hardened gear shafts. This drill not only met the customer’s stringent requirements for high-hardness materials and complex working conditions but also extended tool life to over 250 pieces, significantly outperforming the original branded tools.
I. Project Background: Challenges of High-Hardness Materials and Variable Working Conditions
The part being machined is a transmission gear shaft, which efficiently and stably transfers engine power to the differential and wheels. Due to the complex working environment and high torque loads, the part is made from high-strength alloy steel 10CrMo11 and undergoes nitriding treatment, achieving a surface hardness of HRC58-63, making it a typical difficult-to-machine material.
Machining Parameters:
- Material: 10CrMo11 (nitrided hardened layer HRC58-63)
- Machine Type: Vertical machining center
- Cooling Method: Internal cooling (emulsion)
- Machining Area: ∅10/14 stepped installation hole pilot hole
- Target Tool Life: ≥180 pieces
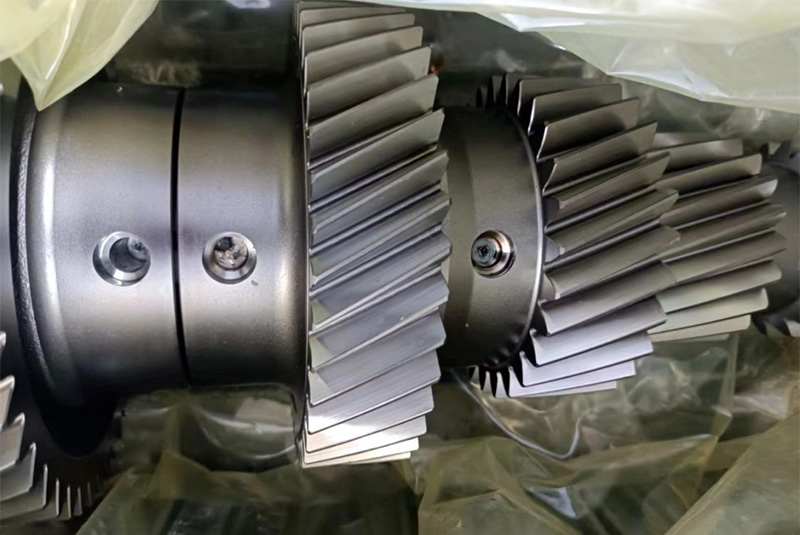
II. Analysis of Machining Challenges
For this project, we identified several key challenges:
- High Difficulty in Machining High-Hardness Materials Both the outer ring and core shaft of the gear are nitrided high-hardness components, causing rapid wear or even chipping of the cutting edge.
- Risk of Tool Breakage Due to Clearance Impact When the drill passes through the clearance between the outer ring and core shaft, the tip experiences strong impact, leading to potential chipping or breakage.
- Insufficient Cooling Affects Initial Cutting Stability With fast machine operation, cooling may not be fully effective during the first hole, causing chip adhesion and built-up edge issues during the initial cutting phase, impacting tool life.
- Strict Cost Control Requires Resharpenable Design The customer is sensitive to overall costs, requiring that the tool must not have severe damage after use to support multiple resharpenings.
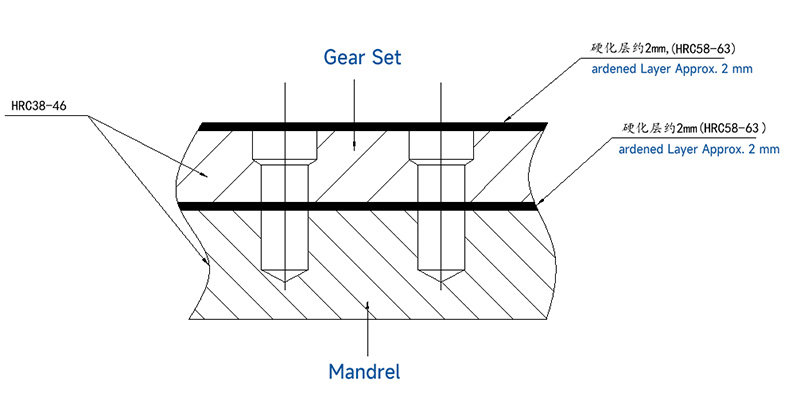
III. Our Solution: SDFTools Custom Step Drill
Based on these challenges, we addressed them comprehensively by optimizing flute geometry, edge treatment, and coating selection, creating a high-performance carbide step drill tailored to the customer’s needs, achieving full-process optimization from design to application.
✅ 1. Optimized Flute and Helix Angle for Smooth Chip Evacuation
- Adopted a double-flute structure (2 CL Slot) combined with a special helix angle design, significantly improving chip flow paths.
- The flutes underwent high-polishing treatment to reduce friction resistance, effectively preventing edge damage caused by poor chip evacuation.
✅ 2. Reinforced Edge Design Balancing Sharpness and Strength
- The rake angle was optimized based on material properties to reduce cutting forces;
- The cutting edge underwent high-polishing + special edge honing, enhancing edge strength while reducing the risk of built-up edge.
✅ 3. Precise Centering Design for Improved Drilling Stability
- The drill’s chisel edge featured a special centering structure, maintaining high positioning accuracy when entering high-hardness materials, avoiding deviation or slippage.
✅ 4. Dual Upgrade of Material and Coating for Extended Tool Life
- Selected high-performance fine-grain carbide substrate, offering excellent wear resistance and impact resistance;
- For the coating, PVD composite coating technology was used, combining high wear resistance with good thermal stability, effectively handling extreme conditions under high-speed dry cutting and internal cooling.
✅ 5. Multi-Step Structure for One-Pass Forming
- To meet the customer’s requirement for ∅9.8mm→∅14mm stepped holes, we designed a dual-step drill structure, completing both diameters in one pass, simplifying the process and improving efficiency.
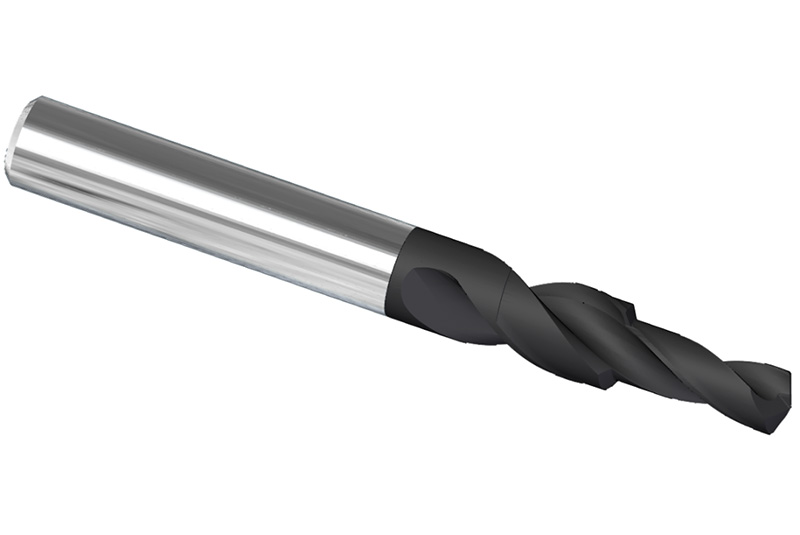
IV. Test Results: Significant Performance Improvement
Under identical machining conditions, we compared the SDFTools custom step drill with the original branded tool:
Item | Original Branded Tool | SDFTools Custom Tool |
Tool Material | Standard Carbide | Fine-Grain Carbide |
Coating Type | CVD Coating | PVD Composite Coating |
Tool Life | 180 pieces | 220–250 pieces |
Life Improvement | —— | +22%~+39% |
Edge Condition | Prone to chipping, significant built-up edge | Sharp with minimal wear |
Resharpenability | Limited to 1 time | Supports 3+ resharpenings |
Additionally, during actual machining, the SDFTools tool demonstrated:
- More stable cutting processes;
- Less vibration and noise;
- Better hole wall quality and consistency.
Customer feedback: “This custom step drill not only exceeded our expectations for machining high-hardness materials but also met our cost control requirements in terms of durability and resharpenability.”
V. Why Choose SDFTools?
🔹Deep Customization Capability
We provide full-process customization services, from drawing analysis, material selection, coating matching, to edge treatment, tailored to customer needs.
🔹 Professional Process Support
We offer trial tooling solutions within 72 hours, with engineers providing full-process follow-up to ensure smooth process adaptation and on-site debugging.
🔹 Quality and Delivery Assurance
Each tool undergoes IPQC/FQC quality inspection, supports global fast delivery, and comes with detailed inspection reports.
🔹 Outstanding Cost-Performance Advantage
Compared to international brands, we offer more competitive pricing while ensuring stable and reliable performance.
VI. Wide Range of Applications, Beyond Automotive Transmission Shafts
In addition to the automotive gear shaft application in this case, SDFTools custom step drills can also be widely used in the following areas:
- Automotive transmission housings, differential components
- Industrial gearboxes, hydraulic valve blocks
- Aerospace structural components
- Precision connection holes in medical equipment
- Complex parts requiring multi-step hole one-pass forming
XI. Contact Us
📧 Email: sdfgroup@sdftools.com
🌐 Website: www.sdftools.com
👥 LinkedIn: Shengdefu Precision Tools Co., Ltd.
Conclusion: Solving Industry Challenges with Professional Customization
This successful case once again demonstrates SDFTools’ technical expertise and market responsiveness in non-standard tool customization. Facing challenges such as high-hardness materials, complex working conditions, and strict cost control requirements, we achieved a win-win solution for efficiency and cost through scientific design, precise material selection, and professional service.
If you have similar machining challenges, feel free to contact our engineering team anytime. Let’s work together to create the most suitable customized tooling solution for you!