Aluminum alloys are typically viewed as relatively easy to machine. However, when it comes to high-silicon aluminum alloys (Si > 12%) , such as ADC12 , the machining process becomes significantly more challenging — especially in high-volume production environments.
Let’s explore a real-world example that highlights this issue.
🔧 Case Study: Face Milling and Drilling of Die-Cast Engine Blocks (ADC12)
A CNC machining facility was assigned the task of performing face milling and drilling operations on die-cast engine blocks made from ADC12 aluminum alloy , which contains 12–15% silicon . While this composition improves casting properties and thermal stability, it also introduces severe challenges for cutting tools.
⚠️ Root Cause: Abrasive Wear Due to Hard Silicon Particles
The primary issue lies in the presence of hard silicon particles (HV1400) embedded within the aluminum matrix. These particles behave like abrasive grit during machining, causing:
- Severe crater wear on the tool’s rake face
- Edge micro-chipping, even with standard PCD (Polycrystalline Diamond) tools
- A drastic reduction in tool life
📉 Quantified Performance Drop:
- A φ20mm endmill lasted less than 15m² of cutting area
- Compared to over 80m² when used on standard aluminum alloys
- That’s just 20% of normal tool life
💸 Cost Implications:
- Tool cost per unit: ¥34.5
- Standard aluminum tool cost: ¥6.8
- This results in a more than fivefold increase in tooling cost per part
🧪 Why Does This Happen? Understanding the Wear Mechanism
High-silicon aluminum alloys contain primary silicon crystals , which are both extremely hard and brittle. During machining, these particles:
- Act like microscopic grinding agents
- Accelerate abrasive wear on both the rake and flank surfaces
- Cause edge chipping , particularly under interrupted cutting conditions
- Reduce overall tool durability, even at lower cutting speeds
Standard PCD tools, although effective for non-abrasive aluminum materials, are not designed to withstand this level of abrasive attack.
✅ The Right Solution: Tools Engineered for High-Si Aluminum Machining
At SDFTools , we specialize in providing cutting tools tailored for the most demanding applications — including the machining of high-silicon aluminum alloys .
Our CVD diamond-coated end mills , developed using advanced coating technology and optimized carbide substrates, offer:
- Exceptional resistance to abrasive wear
- Improved edge strength to prevent micro-chipping
- Carefully engineered tool geometry for stable performance
- Significantly extended tool life compared to conventional options
We have successfully helped numerous customers reduce their tooling costs by up to 70% , while also improving productivity through reduced tool change frequency.
🔬 Recommended Machining Parameters for High-Si Aluminu
Parameter | Standard Aluminum | High-Si Aluminum (ADC12) |
---|---|---|
Cutting Speed | Up to 3000 m/min | Recommended <1200 m/min |
Feed Rate | 0.1–0.3 mm/z | 0.05–0.15 mm/z |
Tool Material | PCD / Uncoated Carbide | CVD Diamond Coated Carbide |
Tool Geometry | Sharp edge | Reinforced edge with honing |
Coolant | Optional | Highly recommended (flood cooling preferred) |
📈 Ready to Improve Your High-Silicon Aluminum Machining Process?
If your production line involves machining components such as:
- Engine blocks
- Transmission housings
- Die-cast parts with high silicon content
And you’re experiencing issues like short tool life , frequent tool changes , or rising machining costs , we can help you optimize your tooling strategy.
👉 Discover our specialized solutions at
https://www.sdftool.com/index.php/customize/
Let us help you turn tool wear into a competitive edge.
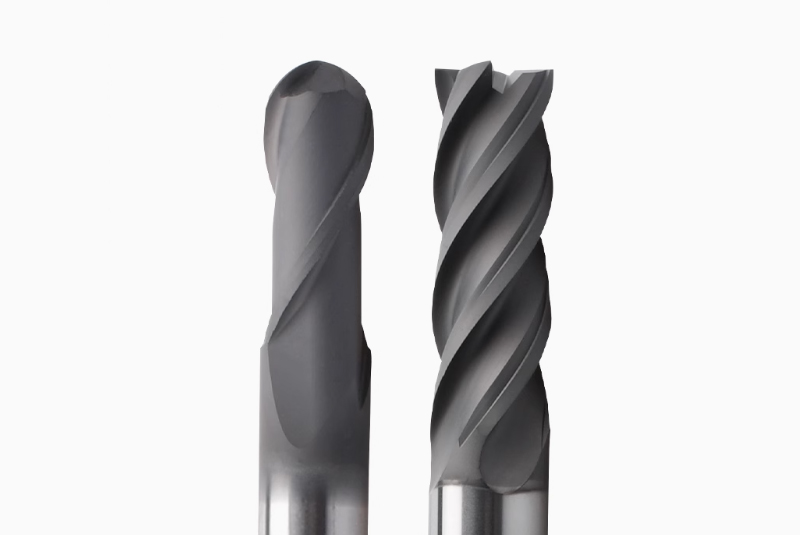